Introduction to Oil Analysis
Oil analysis is one of the most cost-effective predictive maintenance technologies available today. By regularly monitoring the condition of lubricants and the equipment they protect, maintenance professionals can detect problems early, extend equipment life, and prevent costly failures.
What is Oil Analysis?
Oil analysis involves the systematic examination of lubricant samples to determine:
- Oil condition - How well the lubricant is performing its intended function
- Contamination levels - Presence of water, dirt, fuel, or other contaminants
- Wear patterns - Evidence of component wear and potential failure modes
- Additive depletion - Remaining useful life of the lubricant
Benefits of Oil Analysis Programs
Cost Savings
- Reduce unplanned downtime by up to 75%
- Extend oil drain intervals by 25-50%
- Minimize component replacement costs
- Optimize maintenance scheduling
Equipment Reliability
- Early detection of developing problems
- Trend analysis for predictive maintenance
- Improved equipment availability
- Extended component life
Environmental Benefits
- Reduced oil consumption through extended drain intervals
- Proper disposal of contaminated lubricants
- Minimized environmental impact
Key Oil Analysis Tests
Viscosity Testing
Viscosity is the most important property of any lubricant. Changes in viscosity can indicate:
- Thermal degradation - High temperatures breaking down oil molecules
- Oxidation - Chemical reaction with oxygen causing thickening
- Contamination - Fuel dilution reducing viscosity
- Shear breakdown - Mechanical stress reducing viscosity
ASTM Test Methods:
- ASTM D445 - Kinematic Viscosity
- ASTM D2270 - Viscosity Index
- ASTM D5293 - Low Temperature Viscosity
Acid Number Testing
Acid number measures the acidity of the oil, indicating:
- Oxidation levels
- Additive depletion
- Contamination with acidic substances
- Remaining oil life
Normal ranges:
- New oil: 0.5-2.0 mg KOH/g
- Caution level: 2.5-4.0 mg KOH/g
- Critical level: >4.0 mg KOH/g
Water Content Analysis
Water contamination is one of the most damaging contaminants in lubricating systems:
Effects of Water Contamination:
- Reduced film strength - Leading to increased wear
- Corrosion - Attacking metal surfaces
- Additive precipitation - Reducing effectiveness
- Microbial growth - Creating acids and sludge
Acceptable Water Levels:
- Hydraulic systems: <200 ppm
- Gear oils: <500 ppm
- Engine oils: <2000 ppm
Particle Count Analysis
Particle counting measures the cleanliness level of the oil using ISO 4406 standards:
ISO Cleanliness Codes:
- ISO 16/14/11 - Excellent for hydraulic systems
- ISO 18/16/13 - Good for most applications
- ISO 21/19/16 - Marginal, action required
- ISO 24/22/19 - Poor, immediate action needed
Proper Sampling Techniques
Sampling Location
The sampling point is critical for obtaining representative samples:
Best Practices:
- Return lines - Sample from return lines when possible
- Turbulent flow - Ensure oil is well-mixed
- Operating temperature - Sample during normal operation
- Avoid dead zones - Areas where oil may stagnate
Sampling Procedures
Equipment Preparation:
- Use clean, dedicated sampling equipment
- Purge sampling lines before collection
- Label samples immediately
- Document sampling conditions
Sample Volume:
- Routine analysis: 100-120 ml
- Particle counting: 250 ml minimum
- Microscopic examination: 500 ml recommended
Sample Handling and Storage
Transportation:
- Use appropriate containers (plastic for routine tests, glass for fuel dilution)
- Protect from temperature extremes
- Ship within 24-48 hours of collection
- Include proper documentation
Interpreting Oil Analysis Results
Trending vs. Absolute Values
Oil analysis is most effective when results are trended over time:
Key Trending Parameters:
- Viscosity changes - Monitor for increases or decreases
- Acid number progression - Track oxidation development
- Wear metal trends - Identify developing problems
- Contamination levels - Monitor ingression rates
Alarm Limits
Establish appropriate alarm limits based on:
Equipment Criticality:
- Critical equipment: Tighter limits, more frequent sampling
- Non-critical equipment: Standard limits, routine sampling
- Spare equipment: Extended intervals, basic testing
Operating Conditions:
- Severe service: Lower limits, enhanced testing
- Normal service: Standard limits and testing
- Light duty: Extended limits and intervals
Common Oil Analysis Mistakes
Sampling Errors
- Inconsistent sampling points - Use the same location each time
- Contaminated samples - Ensure clean sampling procedures
- Poor timing - Sample during normal operating conditions
- Inadequate documentation - Record all relevant information
Interpretation Errors
- Ignoring trends - Focus on patterns, not single results
- Inappropriate limits - Establish equipment-specific limits
- Delayed action - Respond promptly to abnormal results
- Incomplete testing - Use comprehensive test suites
Implementing an Oil Analysis Program
Program Development Steps
1. Equipment Inventory
- Identify critical equipment
- Determine lubricant types and volumes
- Establish sampling points
- Set sampling frequencies
2. Laboratory Selection
- Choose accredited laboratories
- Verify test capabilities
- Establish reporting formats
- Ensure quick turnaround times
3. Training and Procedures
- Train sampling personnel
- Develop standard procedures
- Establish alarm limits
- Create response protocols
4. Data Management
- Implement trending software
- Establish reporting procedures
- Create action protocols
- Monitor program effectiveness
Success Factors
Management Support:
- Provide adequate resources
- Support training initiatives
- Encourage participation
- Measure program benefits
Technical Expertise:
- Develop internal capabilities
- Utilize laboratory expertise
- Continuous education
- Stay current with technology
Advanced Oil Analysis Techniques
Ferrography
Ferrography provides detailed information about wear particles:
Applications:
- Wear mode identification
- Severity assessment
- Root cause analysis
- Failure investigation
Fourier Transform Infrared (FTIR) Spectroscopy
FTIR analysis detects:
- Oxidation products
- Additive levels
- Contamination types
- Oil degradation
Atomic Emission Spectroscopy
Provides precise measurement of:
- Wear metals
- Additive elements
- Contamination metals
- Oil degradation products
Future Trends in Oil Analysis
Digital Transformation
- Online monitoring systems
- Artificial intelligence interpretation
- Predictive analytics
- Mobile sampling apps
Sensor Technology
- Real-time viscosity monitoring
- Continuous particle counting
- Online water detection
- Temperature and pressure correlation
Data Analytics
- Machine learning algorithms
- Predictive modeling
- Automated reporting
- Integration with CMMS systems
Conclusion
Oil analysis is a powerful tool for optimizing equipment reliability and reducing maintenance costs. Success requires proper sampling techniques, appropriate testing, accurate interpretation, and prompt action on results.
By implementing a comprehensive oil analysis program, maintenance professionals can:
- Detect problems before they cause failures
- Optimize maintenance schedules
- Extend equipment life
- Reduce operating costs
- Improve safety and reliability
The key to success is consistency, proper training, and a commitment to acting on the information provided by oil analysis results.
Additional Resources
For more information on oil analysis best practices, consider these resources:
- ASTM Standards - Comprehensive test methods and procedures
- ISO Standards - International guidelines for oil analysis
- STLE Education - Society of Tribologists and Lubrication Engineers
- Noria Corporation - Training and certification programs
- Professional Certification - Pursue CLS or MLT certifications
Remember, oil analysis is not just about testing oil – it’s about understanding what the results mean for your equipment and taking appropriate action to ensure optimal performance and reliability.
Article Tags
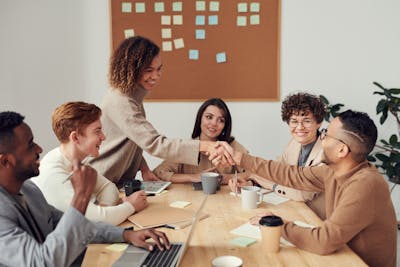
Dr. Sarah Anderson
Dr. Sarah Anderson is a certified lubrication analyst with over 15 years of experience in industrial maintenance and tribology. She holds a Ph.D. in Mechanical Engineering and is a recognized expert in predictive maintenance technologies.