Understanding Hydraulic Systems
Hydraulic systems are the backbone of modern industrial operations, providing precise control and immense power in applications ranging from manufacturing equipment to mobile machinery. Proper maintenance of these systems is crucial for operational efficiency, safety, and cost control.
The Importance of Hydraulic Maintenance
Economic Impact
- Downtime costs can exceed $50,000 per hour in critical applications
- Fluid replacement represents 30-40% of total hydraulic maintenance costs
- Component failures often result from preventable contamination issues
- Energy efficiency improves by 10-15% with proper maintenance
Performance Benefits
- Consistent system pressure and flow
- Reduced component wear and tear
- Extended equipment life
- Improved safety and reliability
Hydraulic Fluid Analysis
Key Parameters to Monitor
Viscosity
Viscosity is critical for proper hydraulic system operation:
Optimal viscosity range: 16-36 cSt at operating temperature
Viscosity changes indicate:
- Increased viscosity: Oxidation, contamination, or wrong fluid type
- Decreased viscosity: Thermal breakdown, fuel contamination, or shear
Cleanliness Level (ISO 4406)
Hydraulic systems require extremely clean fluid:
Target cleanliness levels:
- Servo valves: ISO 16/14/11 or better
- Proportional valves: ISO 18/16/13
- General hydraulics: ISO 20/18/15
Water Content
Water contamination severely impacts hydraulic performance:
Acceptable levels:
- Free water: 0% (none visible)
- Dissolved water: <200 ppm
- Total water: <500 ppm
Effects of water contamination:
- Reduced lubrication effectiveness
- Increased corrosion and wear
- Additive precipitation
- Reduced bulk modulus
Acid Number and Base Number
Total Acid Number (TAN)
- New fluid: <0.5 mg KOH/g
- Caution level: 1.0-2.0 mg KOH/g
- Change fluid: >2.0 mg KOH/g
Total Base Number (TBN)
- Monitor for additive depletion
- Significant decrease indicates fluid degradation
Filtration Systems
Filter Types and Applications
Suction Strainers
- Purpose: Protect pump from large debris
- Mesh size: 100-200 microns
- Maintenance: Clean regularly, replace when damaged
Pressure Filters
- Location: Downstream of pump
- Function: Protect system components
- Rating: 10-25 microns absolute
Return Filters
- Purpose: Clean fluid returning to reservoir
- Rating: 10 microns or finer
- Benefit: Maintains overall system cleanliness
Offline Filtration
- Application: Continuous fluid conditioning
- Capability: Sub-micron filtration and water removal
- Benefit: Extends fluid and component life
Filter Maintenance
Inspection Schedule
- Daily: Visual inspection for leaks and damage
- Weekly: Check differential pressure indicators
- Monthly: Record pressure differentials
- Quarterly: Replace elements as needed
Replacement Criteria
- Differential pressure: Follow manufacturer recommendations
- Bypass indicator: Replace when activated
- Scheduled intervals: Based on operating hours
- Fluid analysis: When contamination levels increase
Contamination Control
Sources of Contamination
Built-in Contamination
- Manufacturing debris
- Assembly contamination
- New component particles
- Solution: Thorough system flushing
Ingressed Contamination
- Atmospheric dust and dirt
- Water from condensation
- Maintenance-induced contamination
- Prevention: Proper sealing and filtration
Generated Contamination
- Component wear particles
- Fluid degradation products
- Corrosion particles
- Control: Regular fluid analysis and maintenance
Contamination Prevention
Reservoir Design
- Proper sizing: 3-5 times pump flow rate
- Baffles: Separate return and suction
- Breather: High-efficiency air filtration
- Drain: Easy fluid sampling and drainage
Maintenance Practices
- Clean work environment: Minimize contamination during service
- Proper tools: Use clean, dedicated equipment
- Fluid handling: Maintain cleanliness during transfers
- Component storage: Protect new parts from contamination
System Troubleshooting
Common Hydraulic Problems
Overheating
Symptoms:
- High fluid temperature (>180°F/82°C)
- Reduced system efficiency
- Accelerated fluid degradation
Causes:
- Excessive system pressure
- Internal leakage
- Inadequate cooling
- Contaminated fluid
Solutions:
- Check relief valve settings
- Inspect for internal leaks
- Clean heat exchangers
- Replace contaminated fluid
Slow Operation
Symptoms:
- Reduced actuator speed
- Poor response time
- Inconsistent performance
Causes:
- Low fluid level
- Clogged filters
- Pump wear
- Internal leakage
Solutions:
- Check fluid level and add if needed
- Replace clogged filters
- Inspect pump condition
- Test for internal leakage
Erratic Operation
Symptoms:
- Jerky or inconsistent movement
- Pressure fluctuations
- Noise and vibration
Causes:
- Air in system
- Contaminated fluid
- Worn components
- Improper fluid viscosity
Solutions:
- Bleed air from system
- Replace contaminated fluid
- Inspect and replace worn parts
- Verify correct fluid specification
Diagnostic Techniques
Pressure Testing
- System pressure: Verify pump output
- Component pressure: Check individual circuits
- Relief valve: Test cracking pressure
- Accumulator: Verify precharge pressure
Flow Testing
- Pump flow: Measure actual vs. rated flow
- Component flow: Check valve and actuator flow
- Leakage: Quantify internal and external leaks
- Efficiency: Calculate volumetric efficiency
Temperature Monitoring
- Fluid temperature: Monitor at multiple points
- Component temperature: Check pumps, valves, and actuators
- Ambient conditions: Consider environmental factors
- Thermal imaging: Identify hot spots and problems
Preventive Maintenance Program
Maintenance Schedule
Daily Checks
- Visual inspection for leaks
- Check fluid level
- Monitor operating temperature
- Listen for unusual noises
Weekly Inspections
- Check filter indicators
- Inspect hoses and fittings
- Monitor pressure gauges
- Test emergency stops
Monthly Maintenance
- Sample fluid for analysis
- Check accumulator precharge
- Inspect cooling system
- Clean reservoir breather
Quarterly Service
- Replace filters as needed
- Calibrate pressure switches
- Test relief valves
- Inspect electrical connections
Annual Overhaul
- Comprehensive system inspection
- Replace wear components
- Update maintenance records
- Review system performance
Documentation and Records
Maintenance Logs
- Daily observations: Temperature, pressure, fluid level
- Service activities: Filter changes, fluid additions
- Problem reports: Issues and corrective actions
- Trend analysis: Performance over time
Fluid Analysis Records
- Test results: Maintain complete history
- Trending data: Track key parameters
- Recommendations: Document laboratory suggestions
- Actions taken: Record maintenance performed
Energy Efficiency Optimization
System Design Considerations
Proper Sizing
- Pump selection: Match flow and pressure requirements
- Reservoir capacity: Adequate volume for heat dissipation
- Piping design: Minimize pressure losses
- Component selection: High-efficiency components
Variable Speed Drives
- Energy savings: 20-50% reduction possible
- Improved control: Better system response
- Reduced heat generation: Lower operating temperatures
- Extended component life: Reduced wear and stress
Operating Practices
Load Management
- Demand-based operation: Run only when needed
- Pressure optimization: Use minimum required pressure
- Flow control: Match flow to application needs
- Standby modes: Reduce power during idle periods
Maintenance Impact
- Clean fluid: Improves efficiency by 5-10%
- Proper filtration: Reduces energy losses
- Component condition: Worn parts increase energy consumption
- System optimization: Regular tuning maintains efficiency
Safety Considerations
Pressure Safety
High Pressure Hazards
- Injection injuries: Fluid under pressure can penetrate skin
- Component failure: Sudden release of stored energy
- Hose failure: Whipping hoses can cause injury
- Hot surfaces: High-temperature components
Safety Procedures
- Lockout/tagout: Proper energy isolation
- Pressure relief: Safely release system pressure
- Personal protective equipment: Use appropriate PPE
- Training: Ensure personnel understand hazards
Environmental Protection
Spill Prevention
- Secondary containment: Protect against leaks
- Spill response: Have cleanup materials ready
- Proper disposal: Follow environmental regulations
- Leak detection: Monitor for fluid losses
Fluid Selection
- Biodegradable fluids: Consider environmental impact
- Fire-resistant fluids: Use where required
- Proper disposal: Recycle or dispose responsibly
- Inventory management: Minimize waste
Conclusion
Effective hydraulic system maintenance requires a comprehensive approach combining regular monitoring, proper filtration, contamination control, and systematic troubleshooting. By implementing these best practices, organizations can achieve:
- Reduced downtime: Prevent unexpected failures
- Lower costs: Extend component and fluid life
- Improved performance: Maintain system efficiency
- Enhanced safety: Protect personnel and environment
The key to success is consistency in maintenance practices, proper training of personnel, and prompt response to fluid analysis results and system indicators.
Best Practice Summary
- Establish baseline conditions through initial fluid analysis
- Implement regular sampling and trending programs
- Maintain proper filtration at all system points
- Control contamination through design and procedures
- Monitor system performance continuously
- Train personnel in proper maintenance techniques
- Document all activities for trend analysis
- Respond promptly to abnormal conditions
Remember, hydraulic system maintenance is an investment in reliability, efficiency, and safety. The cost of proper maintenance is always less than the cost of system failure.
Article Tags
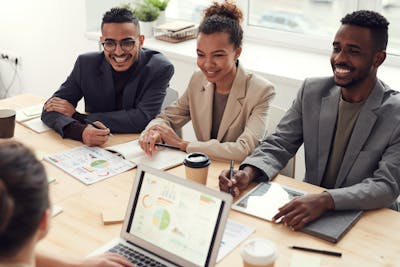
Michael Huff
Michael Huff is a senior hydraulic systems engineer with 20 years of experience in industrial automation and fluid power systems. He specializes in hydraulic system design, troubleshooting, and maintenance optimization.