Introduction to Gear Oil Analysis
Gear oil analysis is a specialized branch of tribology that focuses on monitoring the health of gear systems through systematic examination of lubricant samples. Industrial gearboxes are critical components in manufacturing, power generation, and processing facilities, making their reliable operation essential for productivity and profitability.
Understanding Gear Oil Functions
Primary Functions
Load Carrying
- Extreme pressure protection: Prevents metal-to-metal contact under high loads
- Film strength: Maintains lubricating film under severe conditions
- Shock absorption: Cushions impact loads during operation
Heat Dissipation
- Thermal conductivity: Transfers heat away from contact zones
- Cooling: Removes heat generated by friction and churning
- Temperature stability: Maintains properties across operating range
Contamination Control
- Particle suspension: Keeps wear debris in suspension
- Water separation: Prevents emulsification with water
- Foam suppression: Minimizes air entrainment
Gear Oil Types
Mineral-Based Oils
- Conventional: Refined petroleum base stocks
- Solvent refined: Improved oxidation resistance
- Hydroprocessed: Enhanced thermal stability
- Applications: General industrial gearboxes
Synthetic Oils
- Polyalphaolefin (PAO): Excellent low-temperature properties
- Polyglycol (PAG): Superior thermal stability
- Ester-based: Biodegradable options
- Applications: Severe service conditions
Semi-Synthetic Blends
- Combination: Mineral and synthetic base stocks
- Performance: Enhanced properties at lower cost
- Applications: Moderate to severe service
Critical Gear Oil Analysis Tests
Viscosity Analysis
Kinematic Viscosity (ASTM D445)
Viscosity is the most important property for gear oil performance:
Typical ranges by ISO VG grade:
- ISO VG 150: 135-165 cSt at 40°C
- ISO VG 220: 198-242 cSt at 40°C
- ISO VG 320: 288-352 cSt at 40°C
- ISO VG 460: 414-506 cSt at 40°C
Viscosity changes indicate:
- Increase: Oxidation, contamination, or thermal stress
- Decrease: Shear breakdown, fuel dilution, or base oil volatility
Viscosity Index (ASTM D2270)
- Mineral oils: Typically 90-110
- Synthetic oils: Often >140
- Significance: Temperature-viscosity relationship
Acid Number Testing
Total Acid Number (TAN) - ASTM D664
Measures oil degradation and additive depletion:
Typical progression:
- New oil: 0.5-2.0 mg KOH/g
- Normal service: 2.0-4.0 mg KOH/g
- Caution level: 4.0-6.0 mg KOH/g
- Critical level: >6.0 mg KOH/g
Factors affecting TAN:
- Operating temperature
- Contamination levels
- Oil type and additives
- Service conditions
Wear Metal Analysis
Elemental Analysis (ASTM D5185)
Monitors component wear through metal detection:
Ferrous metals:
- Iron (Fe): General wear indicator
- Chromium (Cr): Bearing races, gear surfaces
- Nickel (Ni): Bearing cages, some gear alloys
Non-ferrous metals:
- Copper (Cu): Bronze bearings, thrust washers
- Lead (Pb): Bearing overlays, bronze alloys
- Tin (Sn): Bearing materials, bronze components
- Aluminum (Al): Some bearing materials, housings
Typical alarm levels (ppm):
- Iron: 25-50 ppm (depending on gearbox size)
- Copper: 10-25 ppm
- Lead: 10-25 ppm
- Chrome: 5-15 ppm
Particle Count Analysis
ISO 4406 Cleanliness Code
Gear oils require specific cleanliness levels:
Target levels:
- Enclosed gears: ISO 20/18/15 or better
- Open gears: ISO 22/20/17
- Critical applications: ISO 18/16/13
Particle size significance:
- >4 μm: General contamination level
- >6 μm: Silt-sized particles
- >14 μm: Large wear particles and debris
Water Content Analysis
Karl Fischer Titration (ASTM D6304)
Water contamination severely impacts gear performance:
Acceptable levels:
- Mineral gear oils: <500 ppm
- Synthetic gear oils: <200 ppm
- Critical applications: <100 ppm
Water contamination effects:
- Reduced film strength
- Accelerated oxidation
- Corrosion and pitting
- Additive precipitation
- Microbial growth
Foam and Air Release
Foam Testing (ASTM D892)
Excessive foaming indicates:
- Antifoam additive depletion
- Contamination with detergents
- Mechanical issues (air ingestion)
- Improper oil selection
Air Release (ASTM D3427)
Important for:
- Hydraulic gear systems
- High-speed applications
- Systems with tight clearances
Advanced Analytical Techniques
Ferrography Analysis
Analytical Ferrography
Provides detailed wear particle information:
Particle types identified:
- Rubbing wear: Normal sliding wear particles
- Cutting wear: Severe abrasive wear
- Fatigue particles: Spalling and pitting wear
- Corrosive wear: Chemical attack particles
Severity assessment:
- Particle concentration: Wear rate indication
- Particle size distribution: Wear mode identification
- Particle morphology: Root cause analysis
Direct Reading Ferrography
Quantitative measurement of ferrous wear:
- DL (large particles): >5 μm ferrous particles
- DS (small particles): 1-5 μm ferrous particles
- Wear Particle Concentration (WPC): DL + DS
- Large Particle Index (LPI): DL/DS ratio
FTIR Spectroscopy
Oxidation Monitoring
Tracks oil degradation through:
- Carbonyl formation: 1700-1750 cm⁻¹
- Hydroxyl groups: 3200-3600 cm⁻¹
- Nitration products: 1630 cm⁻¹
Additive Monitoring
- Antioxidants: Phenolic and aminic types
- Anti-wear additives: Zinc dialkyldithiophosphate (ZDDP)
- Extreme pressure additives: Sulfur and phosphorus compounds
- Antifoam agents: Silicone-based additives
Contamination Detection
- Water: Broad absorption at 3200-3600 cm⁻¹
- Fuel: Aliphatic C-H stretching
- Glycol: Characteristic C-O stretching
- Soot: Broad absorption increase
Microscopic Examination
Particle Identification
Direct observation reveals:
- Wear particle morphology: Shape and surface features
- Contamination types: Sand, dirt, fibers
- Corrosion products: Rust and oxidation particles
- Additive crystals: Precipitated additives
Photomicrography
Documents findings for:
- Trend analysis: Particle evolution over time
- Root cause analysis: Failure mode identification
- Training purposes: Educational examples
- Quality assurance: Laboratory verification
Gear-Specific Failure Modes
Tooth Surface Failures
Pitting
Characteristics:
- Small surface craters
- Fatigue-related failure
- Stress concentration points
Oil analysis indicators:
- Increased iron levels
- Large fatigue particles in ferrography
- Possible increase in particle count
Scuffing
Characteristics:
- Adhesive wear mechanism
- Metal transfer between surfaces
- Severe surface damage
Oil analysis indicators:
- Rapid increase in wear metals
- Cutting wear particles
- Possible viscosity changes
Scoring
Characteristics:
- Abrasive wear mechanism
- Parallel scratches on tooth surfaces
- Progressive damage
Oil analysis indicators:
- Elevated particle counts
- Abrasive wear particles
- Contamination presence
Bearing Failures
Rolling Element Bearings
Failure modes:
- Fatigue spalling: Subsurface crack propagation
- Adhesive wear: Metal transfer and smearing
- Abrasive wear: Contamination damage
- Corrosive wear: Chemical attack
Oil analysis detection:
- Specific wear metal patterns
- Characteristic particle morphology
- Water or acid contamination
Journal Bearings
Failure modes:
- Wiping: Severe adhesive wear
- Cavitation erosion: Bubble collapse damage
- Corrosion: Chemical attack
- Fatigue: Crack propagation
Monitoring parameters:
- Copper and lead levels
- Particle morphology
- Contamination levels
Sampling Best Practices
Sampling Location Selection
Optimal Locations
- Drain valve: During oil changes
- Circulation system: Active oil flow
- Return line: After filtration
- Sump: Representative of bulk oil
Locations to Avoid
- Dead zones: Stagnant oil areas
- Near filters: May not represent system condition
- Sight glasses: Often contaminated
- Fill ports: Potential contamination source
Sampling Procedures
Equipment Preparation
- Clean sampling equipment: Dedicated tools for each system
- Proper containers: Appropriate for planned tests
- Labeling: Clear identification and documentation
- Safety: Follow lockout/tagout procedures
Sample Collection
- Operating conditions: Sample during normal operation
- Purge lines: Clear sampling lines before collection
- Sample volume: Adequate for all planned tests
- Multiple samples: For critical systems
Sample Handling
- Temperature protection: Avoid extreme temperatures
- Contamination prevention: Seal containers immediately
- Documentation: Complete sample information forms
- Transportation: Ship promptly to laboratory
Interpretation Guidelines
Trending Analysis
Establishing Baselines
- New oil values: Document initial properties
- Early service samples: Establish normal wear patterns
- Seasonal variations: Account for temperature effects
- Load variations: Consider operational changes
Trend Evaluation
- Rate of change: Monitor parameter progression
- Correlation analysis: Compare related parameters
- Seasonal adjustments: Account for environmental factors
- Operational correlation: Link to equipment changes
Alarm Limit Development
Equipment-Specific Limits
- Criticality assessment: Adjust limits based on importance
- Operating conditions: Consider severity factors
- Historical data: Use past performance data
- Manufacturer recommendations: Follow OEM guidelines
Multi-Level Alarms
- Normal: Routine monitoring range
- Caution: Increased monitoring frequency
- Critical: Immediate action required
- Emergency: Shutdown consideration
Action Protocols
Routine Monitoring
- Sample frequency: Based on criticality and conditions
- Test slate: Appropriate for application
- Trending: Regular data analysis
- Reporting: Communicate findings
Abnormal Results
- Verification: Confirm unusual results
- Investigation: Determine root cause
- Corrective action: Address identified problems
- Follow-up: Monitor effectiveness
Maintenance Optimization
Oil Change Intervals
Condition-Based Maintenance
- Oil analysis results: Primary decision factor
- Operating conditions: Adjust for severity
- Equipment criticality: More frequent for critical units
- Cost optimization: Balance analysis cost vs. oil cost
Interval Adjustment Factors
- Temperature: Higher temperatures reduce intervals
- Contamination: Dirty environments require more frequent changes
- Load: Heavy loads accelerate degradation
- Water ingression: Moisture contamination shortens life
Filtration Strategies
Offline Filtration
- Kidney loop systems: Continuous oil conditioning
- Portable filter carts: Periodic cleaning
- Vacuum dehydration: Water removal
- Electrostatic separation: Fine particle removal
Filter Selection
- Micron rating: Based on system requirements
- Beta ratio: Efficiency specification
- Dirt holding capacity: Service life consideration
- Bypass protection: Prevent unfiltered flow
Economic Benefits
Cost Avoidance
Failure Prevention
- Unplanned downtime: Avoid production losses
- Emergency repairs: Prevent costly rush repairs
- Secondary damage: Minimize collateral damage
- Safety incidents: Prevent injury and liability
Maintenance Optimization
- Extended oil life: Reduce fluid costs
- Planned maintenance: Schedule during convenient times
- Inventory optimization: Reduce spare parts inventory
- Labor efficiency: Optimize maintenance resources
Return on Investment
Program Costs
- Sampling supplies: Bottles, pumps, labels
- Laboratory analysis: Test costs
- Personnel time: Sampling and interpretation
- Equipment: Sampling tools and storage
Savings Calculation
- Avoided failures: Quantify prevented costs
- Extended intervals: Calculate oil savings
- Improved efficiency: Energy and productivity gains
- Insurance benefits: Potential premium reductions
Conclusion
Gear oil analysis is a powerful predictive maintenance tool that provides early warning of developing problems in critical drive systems. Success requires:
- Proper sampling techniques to ensure representative samples
- Appropriate test selection based on equipment and conditions
- Accurate interpretation of results and trends
- Prompt action on abnormal findings
- Continuous improvement of the monitoring program
By implementing a comprehensive gear oil analysis program, organizations can achieve significant improvements in equipment reliability, maintenance efficiency, and operational costs.
The key to success is understanding that gear oil analysis is not just about testing oil – it’s about understanding the health of the entire gear system and taking proactive steps to ensure optimal performance and longevity.
Best Practices Summary
- Establish consistent sampling procedures and locations
- Use appropriate test suites for your specific applications
- Develop equipment-specific alarm limits based on historical data
- Trend results over time rather than relying on single samples
- Correlate oil analysis with other condition monitoring techniques
- Train personnel in proper sampling and interpretation
- Document all activities for continuous improvement
- Act promptly on abnormal results to prevent failures
Remember, the cost of a comprehensive gear oil analysis program is minimal compared to the cost of a single major gearbox failure. Invest in proper monitoring to protect your critical assets and ensure reliable operation.
Article Tags
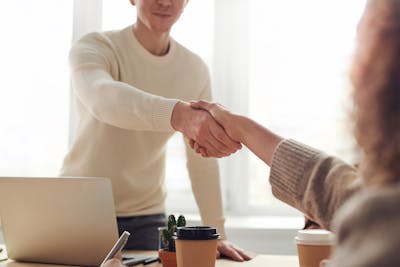
James Muratore
James Muratore is a tribology specialist with 12 years of experience in gear oil analysis and industrial lubrication. He holds certifications in oil analysis and specializes in wind turbine and industrial gearbox maintenance.